Gas Transmitter
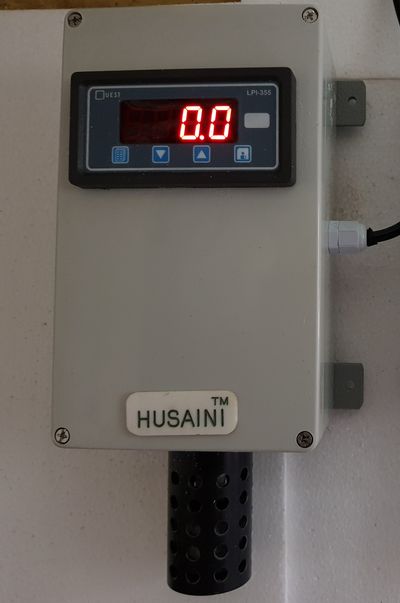
Gas Transmitter
A Gas Transmitter is a device that interfaces with gas sensors to transmit measurement data in the form of a 4-20mA DC current signal. It ensures seamless communication between sensors and control systems such as PLCs, actuators, and panel meters.
Gas transmitters from Husaini® Engineers play a crucial role in industrial process monitoring and control, ensuring accurate data transmission from sensors over distances with minimal signal loss. Designed for two-wire 4-20mA current loop systems, these devices convert sensor signals into reliable control signals, making them indispensable for various industrial applications.
Why Gas Transmitters are Essential?
A Gas Transmitter ensures:
- Accurate representation of sensor signals.
- Seamless integration with control systems.
- Long-term reliability in harsh environments.
By converting real-world sensor signals into actionable data, gas transmitters are the backbone of industrial automation and safety.
Key Features And Functions of Gas Transmitter
Two-Wire Signal Transmission:
- Utilizes 4-20mA DC control loops to transmit sensor signals over long distances with negligible loss.
- Requires only two wires for signal transmission and power supply, reducing installation costs.
24V DC Power Supply:
- Operates on a standard 24V DC power supply, with compatibility for other voltages such as 12V, 15V, and 36V DC.
Proportional Current Output:
- Represents 0% sensor input as 4mA and 100% input as 20mA, ensuring standardized signal interpretation across devices.
- Acts as a variable resistor, adjusting loop current based on sensor input.
Noise and Resistance Immunity:
- Unaffected by electrical noise and changes in lead wire resistance, even in challenging industrial environments.
Advantages of a 4-20mA Current Loop
- Cost Efficiency: Requires only two wires for power and signal, reducing installation and material costs.
- Reliability: Maintains signal integrity over long distances, unaffected by electrical noise or temperature-induced resistance changes.
- Standardized Interface: Ensures compatibility with a wide range of control systems like PLCs, DCS, and actuator systems.
Application
- Chemical Plants: To regulate gas concentrations for safe and efficient processes.
- Oil & Gas: For monitoring hazardous gases and ensuring safety compliance.
- Power Plants: To maintain operational efficiency by monitoring critical gas levels.
- Pharmaceuticals: To control gas flows in precision-sensitive environments.
- Warehousing of Hazardous Materials: Prevents accidents caused by gas leaks or vapour emissions.
Installation & Maintenance Guidelines:
Proper Installation Steps:
- Ensure the apparatus is classified correctly for the operational area and temperature.
- Use appropriate cable types and gland terminations.
- Verify all electrical connections, earthing, and gaskets are secure and intact.
Inspection Checklist:
- Apparatus matches area classification and temperature.
- Electrical connections are tight and secure.
- Cable entries are sealed to maintain enclosure integrity.
- Periodically inspect for corrosion, rust, or damage to enclosures and connections.