Calibration
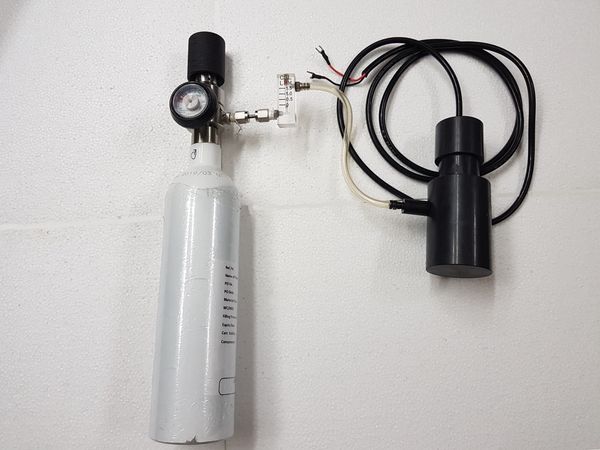
Calibration
Calibration is an essential process to ensure that industrial instruments and devices operate with maximum accuracy, reliability, and safety. At Husaini® Engineers, our specialized calibration services provide comprehensive solutions for a wide array of equipment, including gas detectors, pH controllers, and turbidity sensors. With a commitment to high standards, we guarantee peak performance for your devices while ensuring compliance with regulatory norms.
Our instruments are factory-tested and calibrated to provide unmatched precision and reliability. We also offer calibration tools and expert guidance for on-site calibration. Contact us to learn more about our calibration solutions and keep your operations running smoothly and efficiently.
When is Calibration Required?
Calibration may be necessary under the following circumstances:
- New Instruments: To establish a baseline of accuracy before use which is done at the factory before Dispatch.
- Post-Repair or Modification: Ensures the integrity of measurements after adjustments or repairs.
- Time-Elapsed Calibration: Following a specific time period as recommended by the manufacturer or industry standards.
- Operational Usage: After prolonged operating hours or heavy use.
- Critical Measurements: Before and after significant measurements to ensure accuracy.
- Post-Event: After incidents like physical damage, shocks, vibrations, or sudden weather changes.
- Questionable Observations: When output differs significantly from expectations or surrogate instruments.
- Compliance: As mandated by customer specifications or manufacturer recommendations.
Key Benefits of Calibration:
- Minimized Operational Downtime: Calibration can be performed on-site without requiring hot work permits, reducing disruptions.
- Ease of Use: Instruments are designed with local displays and buttons, enabling calibration without opening the junction box.
- Accuracy Assurance: Aligns the instrument’s output to a known standard, ensuring precision and compliance with specified accuracy.
Calibration Procedure
Calibration at the field can be conducted using a high-pressure canister of known PPM (parts per million) in a calibration chamber. Below is a step-by-step overview:
- Preparation: Ensure the instrument is turned on and connected to the sensor. The display should show a zero reading.
- Set the Calibration Chamber: Insert the tubing, align the chamber and secure it with the Canister C10 Valve.
- Seal the Sensor: Remove the sensor guard and place the sensor inside the calibration chamber. Seal tightly to ensure it is leak-proof.
- Introduce the Calibration Gas: Open the C10 Valve slowly, view the flow at flowmeter having constant flow of 1 LPM and allowing the calibration gas to diffuse into the chamber.
- Read and Adjust: Check the display. If the reading does not match the PPM of the canister value, adjust Pot-4 until the reading aligns accurately.
- Completion: The instrument is now calibrated and ready for use.
Importance of Calibration:
- Enhanced Accuracy: Ensures reliable measurements, especially in critical applications.
- Extended Instrument Life: Regular calibration helps maintain the integrity of the sensor and overall equipment.
- Safety Compliance: Meets industry standards and regulatory requirements for operational safety.
- Efficiency: Reduces measurement errors that could lead to costly downtime or equipment damage.